Surfaces with thicknesses designed to direct the flow front either by attracting the flow with leaders or by deflecting the flow with deflectors.
As indicated by the yellow arrow in the following diagram, flow leaders are thicker parts of the cavity, which attract the flow. As indicated by the red arrow in the following diagram, deflectors are thinner parts of the cavity which constrict the flow and slow it down.
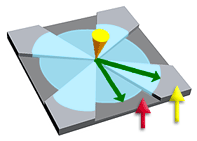
- The thickness change in a flow leader or flow deflector should not be greater than 25% of the wall thickness.
- There should be a gradual change in thickness between the flow leader/deflector and the surrounding part. The diagram above is stepped, but this is for illustration purposes.
- Cooling times for the part might be lengthened if the flow leader is the thickest section of the part.
- Strength of the finished part might be compromised if a flow deflector is used in a critical section of the part.
|
Advantages |
Disadvantages |
Flow leaders
|
- Reduce shear stress level in the part.
- If flow leaders were not initially part of the design, flow leaders are easily created because they are created by removing steel from the mold.
|
- Flow leaders add material to the part.
- Potentially the cycle time is increased if the flow leader is the thickest area on the part.
|
Flow deflectors
|
- Flow deflectors reduce the wall thickness, saving material.
- May reduce cycle time.
|
- Potentially the structural integrity of the part could be compromised so care must be taken if wall thicknesses are reduced to balance the flow or move a weld line.
- Increases shear stress in the part.
|