Use Level of Detail representations to specify which components are loaded in memory or to create a single part representation. You can create several representations to load different aspects of the assembly, as well as manage memory consumption.
At any time, you can change to a different Level of Detail representation. Double-click its name in the browser to activate it, or if you prefer, right-click the name and select Activate.
Examine the system-defined Level of Detail representations
All assemblies contain five system-defined Levels of Detail:
- Master (the default)
- All Components Suppressed
- All Parts Suppressed
- All Content Center Suppressed
- All On
To open a file with either a system-defined or user-defined Level of Detail active, click Options in the File Open dialog box, select the desired Level of Detail, then click Open. Examine the effects of one of the system-defined Level of Detail representations using one of your own assembly files or one of the sample model files.
Note: The system-defined Level of Detail representations are only available for files migrated and saved to the current release. If necessary, open the assembly and then click Save. In the Save dialog box, click Yes to All (to save all files) and then click OK. Close and reopen the assembly.
- Open an assembly file, for example, the sample file Engine.iam.
- In the browser, click to expand the Representations folder, and then click to expand the Level of Detail folder.
By default, the Master representation is selected and all components in the assembly are loaded into memory. Scroll down the browser hierarchy to see that all files are listed.
- In the browser, double-click the All Content Center Suppressed representation. In the Engine.iam example, some of the washers and bolts are removed from memory and the graphics window. Scroll down the browser hierarchy to see that the content center components are suppressed (shown as strike-through text).
Note: The All Content Center Suppressed representation suppresses all components saved in the following two locations: Default Content Center Files folder specified on the File tab of the Application Options dialog box, and Content Center Files folder specified in Folder Options of the current project. If a Content Center component is not saved in either of these two locations, it is not suppressed.
- Double-click either All Components Suppressed or All Parts Suppressed, and then scroll down the browser to see the results. All parts or components are removed from memory and the graphics window.
Tip: You can open an assembly with one of the system Level of Detail representations activated. In the file Open dialog box, select the assembly to open, and then click Options. On the File Open Options dialog box, select a system Level of Detail representation.
Note: Check the capacity meter on the status bar to see the number of occurrences and files loaded with each representation.
Create a Level of Detail representation with a reduced number of components
- Click Open and browse to the assembly you want to open.
- In the browser (or in the graphics window, if components are visible), determine which components to suppress or unsuppress.
- Right-click a component in the browser or graphics window, if visible, and select Suppress. If applicable, clear the check mark on Suppress to load the component.
- Continue to Suppress or unsuppress components as needed.
- Right-click the Level of Detail node in the browser, and select New to create a new Level of Detail representation that captures the current suppression states of the components.
- When you finish, click Save to save the file. You are prompted to enter a descriptive name for the new Level of Detail representation.
Note:
- Use the context menu options to create new Level of Detail representations and copies of existing Level of Detail representations.
- You can copy Design View representations into Level of Detail representations. Right-click the Design View representation you want, and select Copy to Level of Detail.
- You can delete user-defined Level of Detail representations. You cannot delete a system-defined representation. Right-click the Level of Detail representation you do not want, and select Delete.
- To open a file with a system-defined or user-defined Level of Detail active, choose Options in the File Open dialog box and select the appropriate Level of Detail before choosing open.
Create a Substitute Level of Detail using Shrinkwrap
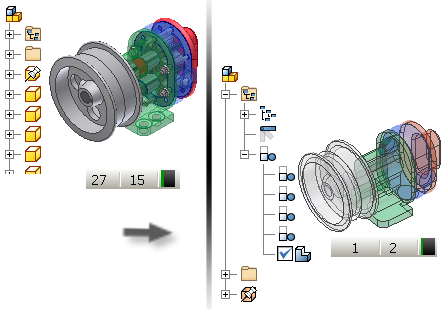
- (Optional) Calculate the Mass Properties of the assembly to include them in the substitute.
- (Optional) Create a Design View or LOD representation that contains only the required components.
- (Optional) Activate the representation.
- Start the Shrinkwrap command.
- In the Shrinkwrap dialog box, the
Components tab is active.
- In the
Representation section, select the Design View, Position, and Level of Detail to be used. If you want the shrinkwrap component to remain associative to the design view in use, check the box.
Note: You can change representations during the create process and the display updates to represent the selected representation. The representation change is a realtime preview and thus changes the model content per the representation. Clicking Cancel does not revert the change. You must specify the desired representation before exiting the dialog box.
- In the
Remove Parts section, if you want to
Remove parts by size check the option and specify the distance of the component bounding box diagonal to use as a filtering criteria. Parts with a smaller or equal measurement are removed.
Note: Entering a value automatically updates the scene.
- In the Include Components section, click
Select to Exclude and in the graphics area select components that are not to be included in the shrinkwrap part.
- By default
View Included is the active display. All components included in the new part display. Change to
View Excluded to see the parts you have selected to not participate. Use the display toggle to help manage the selection process.
- Use the
Selection priority to select
Parts (default) or
Components (parts or assemblies).
- Check
All Occurrences if you want to select all of the occurrences of one part in the selection.
Note: When you change between View Included and View Excluded, dialog labels update to show context and the display updates to match the conditional state.
- Click
Features tab to access options for removing solid features which helps simplify the result.
- In the
Remove Features section, specify the feature types (Holes, Pockets, Fillets, or Chamfers) you want removed from the shrinkwrap part. For each of the feature types you can select:
None of the feature types will be removed.
All of the feature types will be removed.
Remove by range all of the feature types. Those within the range you provide are removed. You can change the value during the creation and edit processes, re-detect features and change the result.
Use the Select tool to pick a feature, the feature is evaluated and a maximum input value extracted. All similar features less than or equal to the Max value are selected.
- Click
Detect Features to highlight all of the selected feature types matching the criteria.
- Click
Preserve Features and click on highlighted features to prevent them from being removed. It is necessary to refresh your selections if Detect Features is clicked. Added components do not automatically have their features selected.
- Click the
Create tab.
- Specify the Part Name, if different from the default, the Template type, file location, and BOM structure to use.
- In the
Style area, select one of the following options:
- Select
Single solid body merging out seams between planar faces to create a solid with no visible edges between planar faces.
- Select
Solid body keep seams between planar faces to create a single solid with visible edges between planar faces.
- Select
Maintain each solid as a solid body to create a multi-body part that contains a unique body for each part in the assembly.
- Select
Single composite feature
(default selection) to create a surface composite body. This option offers the fastest calculation time and creates the smallest file on disk.
- In the
Other Settings, specify:
- Click OK to finish the command and create the substitute. If the mass properties are up to date and the active LOD is not the Master LOD, you are prompted to copy the Mass Properties of the Master or the active LOD before proceeding.
Note: When you create a shrinkwrap part from an assembly and use it as a Substitute, all external reference links are disabled and you must update them manually.
Create a Substitute Level of Detail representation using Derive Assembly
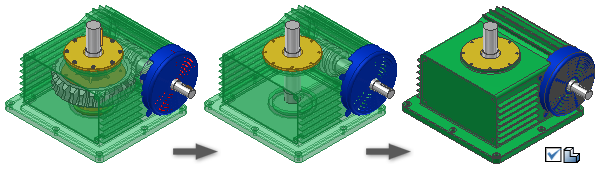
- Click Open and browse to the assembly you want to open.
- To use a reduced part count Level of Detail for the derived assembly, create it before proceeding. This provides the maximum memory savings. You can also proceed to the next step without creating a new Level of Detail.
- Right-click the Level of Detail node in the browser, and choose New Substitute > Derive Assembly to create a new derived part from the assembly. The Level of Detail active at the time of creation contains the default body representation for the derive operation.
- In the New Derived Substitute Part dialog box, name the component, select a template to use if appropriate, and assign the new file location. Click OK to continue.
- A temporary window running the Derived Assembly command is opened. The derived assembly bodies in the list depict the Level of Detail active at the time of creation.
- Select the Bodies tab, the Other tab, or the Representations tab in the Derived Assembly dialog box to make changes before continuing.
- Reduced Memory Mode is on by default. A derived part created using this mode uses less memory by not caching any source bodies. We recommend that you leave this option on.
- Click OK to create the derived part, mark the new part as a substitute, close the derived assembly window and return to the owning (source) assembly.
- The capacity meter in the owning assembly reflects a single part. The Level of Detail browser contains a new active node represented by the Substitute Level of Detail icon.
Note: When you create a derived part from an assembly and use it as a Substitute, all external reference links are disabled

and you must update them manually.
Create a Substitute Level of Detail representation using a part file on disk
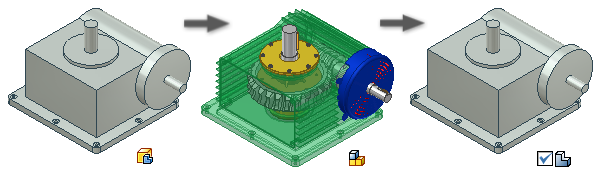
- Create a simplified representation of the assembly by modeling a part or by creating a derived part from an assembly. Save the file to disk.
- If necessary, open the part file on disk.
- Right-click the part node in the browser and select Substitute from the context menu. A dialog box is displayed. If you designate the part as a Substitute, all external reference links are disabled and you must update them manually.
- Click Yes to continue. The part is designated a Substitute and the substitute part icon is attached to the part icon in the browser
. Save the file.
- Open the assembly to be simplified (owning assembly).
- Right-click the Level of Detail node in the browser and select New Substitute> Select Part File.
- In the Place Component dialog box select the simplified part file to use as the substitute, and then click Open.
- The Level of Detail browser node displays the Substitute icon
and the name SubstituteLevelofDetail1. As with other browser entries, you can rename the Substitute Level of Detail.
Note: If the substitute part is not created in the same XYZ location and orientation as the assembly, it is inserted into the assembly in a different position than the assembly it is replacing. Use Grip Snaps or apply constraints to the origin work features to re-position the part. This extra work can be avoided if the substitute part is created from edges or sketches projected from the detailed assembly or is based on surfaces and bodies copied from the detailed assembly.
Note: When you create a derived part from an assembly and use it as a Substitute, all external reference links are disabled

and you must update them manually.
Use the capacity meter to manage memory consumption
To improve performance when working on a large assembly, use the capacity meter to determine the current state of memory consumption. When you want to reduce memory consumption, determine if you can suppress some components and create a new Level of Detail representation or use a Substitute Level of Detail to reduce memory consumption even further.