Troubleshooting air trap problems
Air traps occur when converging flow fronts surround and trap a bubble of air.
The trapped air can cause incomplete filling and packing, and will often cause a surface blemish in the final part. Air trapped in pockets may compress, heat up and cause burn marks.
Causes
- Racetrack effect. The racetrack effect occurs when molten plastic flows into thicker regions more easily than thin regions. The flow divides and then fills thicker sections before combining again to fill the thinner sections. The recombined flow can reverse to meet the oncoming flow in the thinner section.
- Hesitation. In a part with multiple flow paths, the flow can slow down or hesitate in thin regions.
- Unbalanced flow paths. Flow paths do not need to exhibit the racetrack effect or hesitation to have unbalanced flow. In a part with uniform thickness, the physical length of flow paths may vary, and again, air traps may occur.
- Inadequate venting. Lack of vents or undersized vents in these last-to-fill areas are a common cause of air traps.
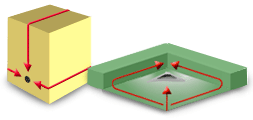
Remedies
- Balance flow paths.
- Avoid hesitation and racetrack effects.
- Balance runners. Changing the runner system can alter the filling pattern in such a way that the last-to-fill areas are located at the proper venting locations.
- Vent appropriately. If air traps do exist, they should be positioned in regions that can be easily vented or ejection and/or vent pins added so that air can be removed.
Solving one problem can often introduce other problems to the injection molding process. Each option hence requires consideration of all relevant aspects of the mold design specification.