Troubleshooting brittleness problems
A brittle molded part has a tendency to break or crack.
Brittleness results from shorter molecular chain length (thus lower molecular weight). As a result, the physical integrity of the part is substantially less than the specification.
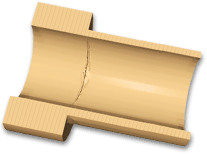
Causes
- Material degradation. This can be caused by excessive injection speed, residence time or melt temperature. Improper screw or runner system design may also lead to material degradation.
- Weld line weaknesses.
- Non-optimal crystallinity.
- High residual stress.
- Incompatible materials blended together.
- Too much regrind.
- Improper drying conditions. Excessive drying either drives off volatiles in the plastic, making it more sensitive to processing, or degrades the material by reducing the molecular weight.
Remedies
- Set proper drying conditions before molding. Material suppliers can provide optimum drying conditions for the specific materials.
- Reduce the regrind material. Contact material suppliers to get the recommended levels of regrind to use.
- Use a different material.
- Optimize the runner system design. Restrictive sprue, runner, gate, or even part design could cause excessive shear heating that aggravates an already overheated material, causing material degradation.
- Modify the screw design. Contact material/machine suppliers to get the right screw design information to avoid improper melt mix or overheating that leads to material degradation.
- Select a machine with smaller shot size. Minimizing residence time reduces material degradation.
- Reduce the residual stress.
- Strengthen the weld lines. Increase melt temperature within limits, not to overheat the material.
Solving one problem can often introduce other problems to the injection molding process. Each option hence requires consideration of all relevant aspects of the mold design specification.