Troubleshooting fish eyes problems
Fish eyes are a surface defect that results from unmelted material being pushed with the melt stream into the cavity and appearing on the surface of a molded part.
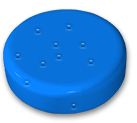
Causes
- Low melt temperature. If the melt temperature is too low to melt the material completely, the unmelted pellets will merge with the melt stream, marring the surface of the part.
- Too much regrind. The shape and size of regrind is irregular compared with original material, and can trap more air and cause the material to blend unevenly.
- Incompatible materials blended together.
- Low screw rotation speed. If the screw rotation speed and the back pressure setting are set too low, there might not be enough shear heating to melt the material completely in the barrel before the injection.
Remedies
- Reduce regrind material. Contact material suppliers to get the recommended levels of regrind to use.
- Optimize melt temperature.
- Modify screw design. Contact material suppliers to get the right screw design information to avoid improper melt mix or overheating that leads to material degradation.
Solving one problem can often introduce other problems to the injection molding process. Each option hence requires consideration of all relevant aspects of the mold design specification.