Troubleshooting flashing problems
Flashing occurs when a thin layer of material is forced out of the mold cavity at the parting line or ejector pins location.
This excess material remains attached to the molded article, and normally has to be manually removed.
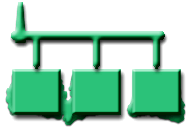
Causes
- Worn or poorly fitted cavity/mold plates. Possible causes include mold plate deformations and obstructions (grease, dirt, debris).
- Insufficient clamp force. The machine clamp force must be greater than the pressure in the cavity (that is, clamp opening force), to sufficiently hold the mold plates shut.
- Overpacking. Overpacked sections cause increased localized pressure.
- Non-optimal molding conditions. Possible causes include material viscosity, injection rate, and runner system design. For example, a high melt temperature results in a less viscous melt.
- Improper venting. Examples include an improperly designed venting system, an ineffective venting system, or a venting system that is too deep.
Remedies
- Ensure the mold plates are correctly fitted, and set up the mold so that it seals properly. Clear any obstructions from the machine. If deformation of a mold plate occurs during the molding process, add a pillar support or thicken the mold plates.
- Avoid overpacking.
- Select a machine with higher clamp force capability.
- Vent appropriately. Use the material supplier's recommended venting size.
- Optimize processing conditions. Reduce pressures and shot size to the minimum required.
Solving one problem can often introduce other problems to the injection molding process. Each option hence requires consideration of all relevant aspects of the mold design specification.