Hydraulic separation provides flow and pressure loss calculations for piping loops.
When you separate hydronic piping systems into primary, secondary, and tertiary loops, calculated flow and pressure loss calculations for each additional loop display on the pump for that loop. The aggregate of the flow values displays on the pump or pump set in the primary loop. The pressure drop reported for a pump reflects the portion of the piping network the pump feeds. As a result, the pump on a primary loop reports the pressure drop for the primary loop. The pump on a secondary loop reports the pressure drop for the secondary loop, and so on.
Note: To use the Add Separation tool, you must enable analysis for closed loop hydronic piping networks on the Hydronic Networks tab in the Mechanical Settings dialog. See
Specify Calculation.
Hydronic piping networks are defined as having:
- A single source equipment component, such as a boiler or chiller. This component is optional.
- A single pump or pump set per loop (primary, secondary, tertiary, and further) if you want to calculate flow and pressure drop for each loop.
- Any number of loads, such as radiators or fan coil units on the secondary and/or additional loops. Radiators and other terminals can be piped in series.
- Any number of pipe segments in the supply sections and return sections of the network.
- The primary loop configured in a loop or using a header.
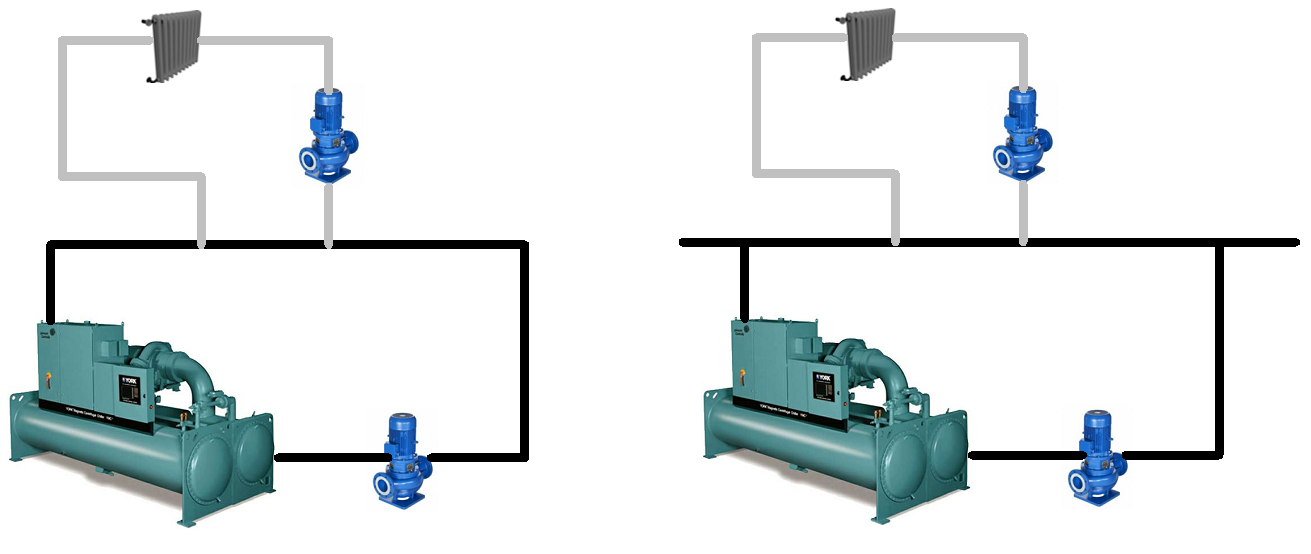
Hydronic networks before separation - primary loop (left) and primary loop with low loss header (right)
Loops are separated analytically: the secondary loop from the primary, the tertiary from the secondary, and so on, as needed. Each loop is assigned to its own system for supply and return. As a result, the primary and secondary systems use the same system type, but are assigned different system instances. The System Name of the secondary systems is appended with a period followed by a number. For example, a network consisting of one primary loop and two secondary loops uses a supply system named Hydronic Supply 1. After hydraulic separation, the network consists of a primary loop that named Hydronic Supply 1 and two secondary loops named Hydronic Supply 1.1 and Hydronic Supply 1.2.
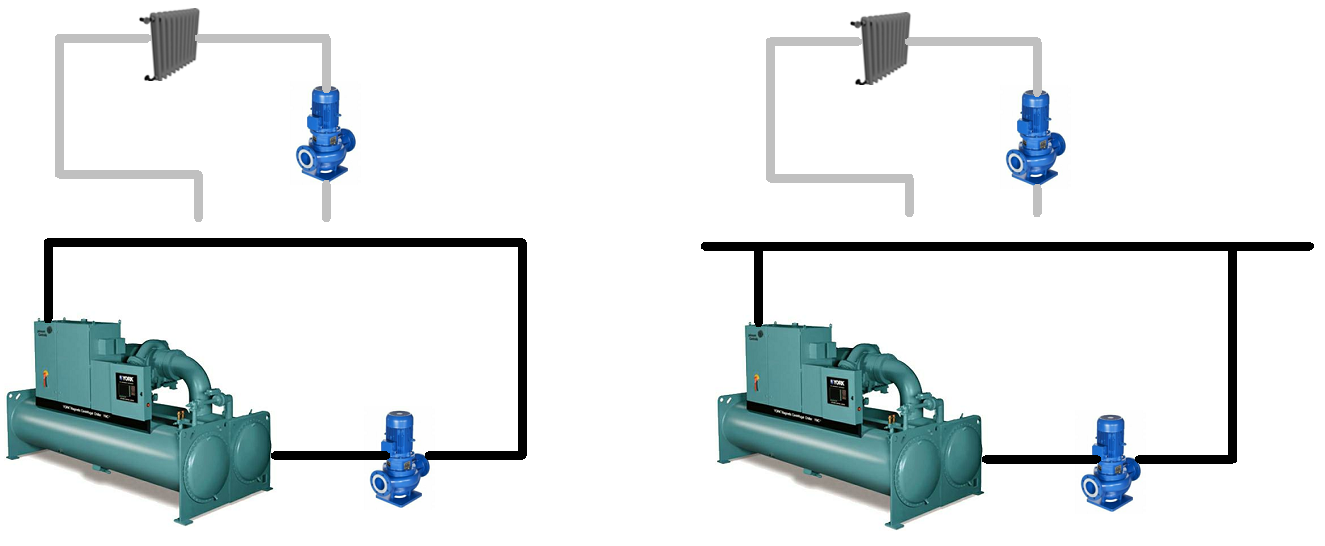
Hydronic networks after separation - primary loop (left) and primary loop with low loss header (right)
Networks may be configured in parallel or series secondary zones:
- Parallel zones are piped so that the primary loop is divided into several crossover branches which serve the secondary zones through closely spaced tees. In this case, there is a common pipe for each secondary loop.
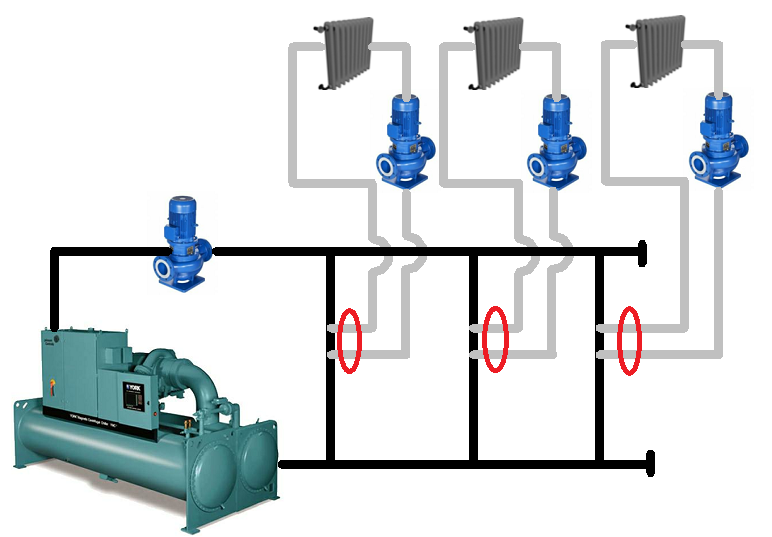
Primary loop with crossover bridges - red indicates which pipes are selected for separation
- The flow in a one-pipe primary is equal to the highest flow of the connected secondary loops. The flow in the common pipe associated with the secondary loop with the highest flow displays zero for flow and the common pipes of the other secondary loops will display a flow that is the difference between the primary and that secondary.
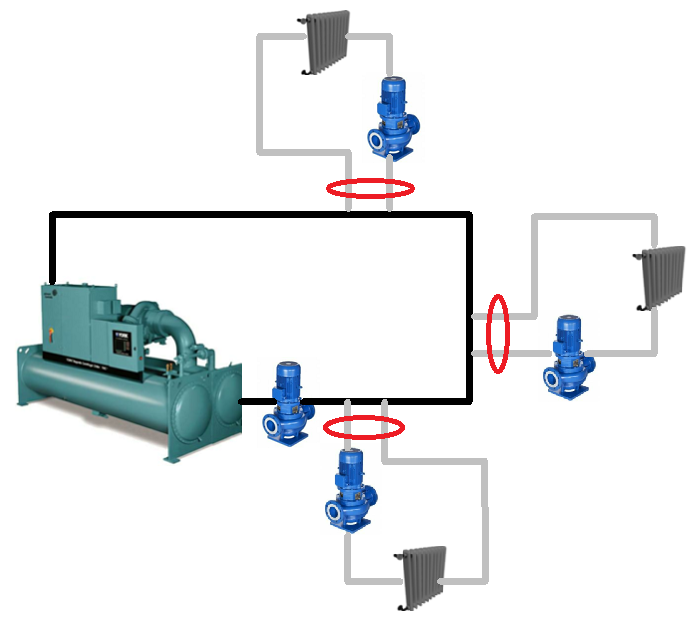
Primary loop with secondary loops with direct and/or reverse return networks - red indicates which pipes are selected for separation
Networks may also be configured so that the primary loop feeds into a low loss header connected to the secondary loops. The section of the header in the center of the secondary connection is the common pipe. This pipe displays zero for flow. When you use the
Pipe Sizing tool, the entire header is sized based on the largest flow at any point in the header.
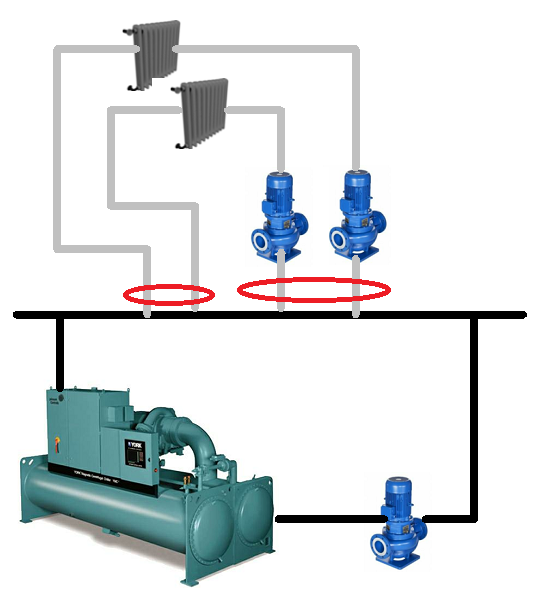
Primary loop with a low loss header - red indicates which pipes are selected for separation
If the secondary loops are connected to the header using tap connections, the header will contain both the supply and return systems of the primary loop. These systems will be divided in the center of the pipe as shown by the tags in the image below. Note that both system names and system classifications are displayed in the Properties Palette.