Nonlinear Solution Control Parameters
Modify the default settings that control the nonlinear solution processes.
Helius PFA significantly improves the overall convergence rate and robustness of progressive failure simulations of composite structures. However, to take full advantage of the superior convergence characteristics, you must change some of the default settings that govern the nonlinear solution process used by ANSYS. This section discusses the use of the ANSYS Mechanical APDL to make the recommended changes to the parameters that govern the nonlinear solution process used by ANSYS. These changes can be enacted using the NROPT, PRED, NSUBST, CNVTOL, and NEQIT commands.
Regardless whether the SOLCONTROL command is ON (default) or OFF, you will need to override these nonlinear solution control parameters.
- NROPT
The NROPT command is used to do two things: a) instruct ANSYS to use the 'Full' Newton Raphson algorithm, and b) prevent ANSYS from using their 'Adaptive Descent' algorithm to help the solution process. The NROPT command can only be specified via the ANSYS command prompt. The image below shows how to type this command into the command prompt.

In ANSYS, the nonlinear solution process is based on the fundamental assumption of the Newton-Raphson algorithm that the nonlinear response of the composite structure is sufficiently smooth at both the global and local levels. However, in a progressive failure simulation, the nonlinear response of the composite structure is not smooth, especially at the local level where material failure results in an instantaneous reduction of material moduli. This non-smooth material response is one of the primary factors responsible for the difficulty in obtaining convergence in progressive failure simulations.
Helius PFA's method of managing material nonlinearity is specifically designed to handle this localized non-smooth material response. However, the default settings of ANSYS' nonlinear solution control parameters must be changed to allow
Helius PFA to improve the convergence characteristics of the simulation.
- PRED
The PRED command prevents ANSYS from using the converged solution at the last substep to estimate the solution for the current substep. This interferes with
Helius PFA's method of managing material linearity. The image below shows how to access this command via the ANSYS Mechanical APDL. As seen below, the "DOF solution predictor" drop-down menu needs to have "Off" selected.
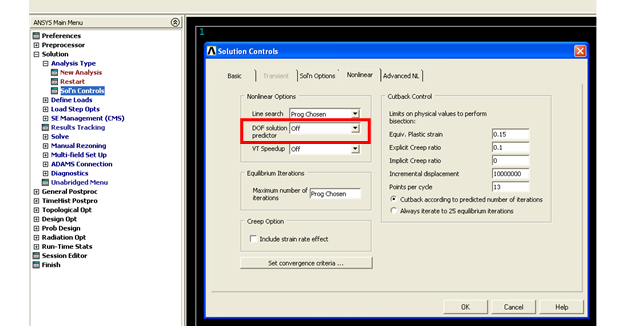
- NSUBST
The NSUBST command specifies the minimum and maximum allowable number of substeps for the current load step. Autodesk does not recommend any minimum or maximum values and engineering judgment should be exercised. However, provided that enough equilibrium iterations are allowed per substep (discussed under NEQIT heading),
Helius PFA will always find a converged solution. This is a deviation from typical nonlinear solution processes where multiple substep size cutbacks may be required.
Helius PFA will converge at each substep, regardless of the size (again provided that enough equilibrium iterations are allowed per substep), so care must be taken when deciding on substep size. The image below displays where to specify the number of substeps in the ANSYS Mechanical APDL.
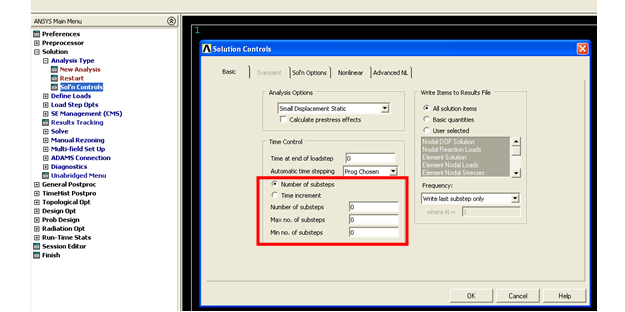
- CVNTOL
The CNVTOL command is used to define the convergence tolerance for residual node forces. There are two arguments set in this command that allow
Helius PFA to better handle the nonlinear solution process: a) set forces (F) as the convergence label, and b) set the norm selection to infinite norm (check each DOF separately). The image below displays where to set these arguments in the ANSYS Mechanical APDL.

- NEQIT
The NEQIT command is used to specify the minimum number of equilibrium iterations that must be performed before ANSYS evaluates the need for cutting-back the size of the current substep.
Helius PFA has the unique ability to converge regardless of the substep size or extent of nonlinearity occurring during the substep. In the experience of Autodesk, convergence always occurs when the number of equilibrium iterations allowed per substep, before a substep cutback occurs, is set to 1000. The image below displays how to set this argument via the ANSYS Mechanical APDL.
