The Simplify command creates either a derived solid or a derived surface composite part from an assembly.
What's New:
2022,
2023,
2024,
2024.2
Use the Simplify command to reduce the content within an assembly by removing components, features, and output a simplified part file. When the command starts the active model state, design view, and position view populate the Initial State group. From there you refine the parameters that define the simplified model. As you select options, other options that are invalid are hidden.
The Simplify command is used to both create and edit simplified parts. Legacy shrinkwrapped parts use the Simplify property panel when edited.
The Simplify command is not accessible when the model is in Express mode.
When accessed from the
BIM Content environment, theOutput Type is locked to Substitute. See step 7 below.
Tip: If you prefer to use <Enter> when inputting values we recommend deselecting the Advanced Setting
Single ENTER to finish command. The default (selected) state uses <Enter> as the OK button to complete the command and commit the changes.
- In the Assemble tab
Simplification panel click
Simplify. The Simplify property panel displays.
- Optionally, select a built-in preset to use. Four built-in presets are provided, plus you can create your own. Presets assign values to the fields further in the property panel. You can override any value.
- Remove the least detail
(small parts and features) - the settings are designed to remove small parts and features, resulting in the most detailed model.
- Remove moderate detail
(medium sized parts and all listed features) - the settings are designed to remove a moderate amount of detail.
- Remove the most detail (replace top-level components with envelopes) - the settings are designed to remove the greatest amount of detail resulting in very basic shapes.
- No Simplification - the simplified version is full fidelity with respect to the assembly model. All details are visible in the model.
Tip: Select a preset close to what you want for detail, then use View Included and View Excluded to quickly select the remaining parts to expedite the process.
The same method can be used for creating your own presets. For more information see
To Work with Presets.
- In the
Input group, fields populate with the current state of the assembly. You can change them as needed.
Model State. The active model state contains the components that define the envelope size. Changes in a model state affect the envelope size.
View. The active design view displays. Changes in design views do not affect envelope size.
Click the
Associative option to link the simplified model to the design view. The option is not available with the Master design view.
Note: When Associative is selected, the Components group is not available as all component changes come from the design view.
Position. Component position contributes to defining the envelope size. Changes in position view can affect the envelope size.
- Replace with Envelopes provide the means to replace components with simple shapes. When you click on an option, preview shows the parts represented as envelopes.
Tip: Combine the use of Presets, Replace with Envelopes, Exclude Components, and Remove Features to refine the simplified model you want to output.
- Exclude Components - provides options for selecting components to include in or exclude from the simplified part. Select individual components or all occurrences of a component.
- Remove Features provides options for selecting features by type and size to include in or exclude from the simplified part. The list of features include holes, fillets, chamfers, pockets (subtractive), embosses (additive), and tunnels (single and multiple entry). Internal voids are automatically removed.
- Pocket recognizes
subtractive features such as extrudes, revolves, sweeps, and so on.
- Emboss recognizes
additive or
positive protrusions of various feature types.
- Tunnel recognizes a set of faces contained inside the model that define an open area, having one or more entrances to the area from exterior faces.
For each of the listed feature types specify which you want to remove and the way you want to remove them:
- Output provides options to define the output type and structure for your intended use.
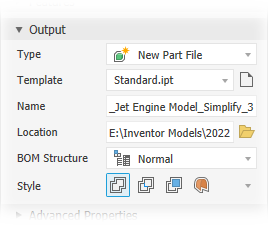
- Type - three output choices are provided:
- New Part File outputs an Inventor part based on the selected template.
- Substitute outputs a simplified Inventor part that populates a Substitute Model State.
Note: When the active model state is a substitute, the Simplify command is not available.
Note: In the BIM Content environment, Substitute is the only Output Type available.
- Revit Model
(RVT) outputs your Inventor design as a Revit model (RVT).
Model orientation: The export process looks at the Inventor ViewCube Top and the Inventor Y-axis. If the Y-axis is perpendicular to the Top plane, the model is rotated so the Inventor Z-axis is perpendicular to the View Cube Top plane.
- Template - sets the part template file to use for the new part file output. Choose between Sheet Metal or Standard part templates, or navigate to a custom template. If the template field is empty an alert will show next to the field.
Note: Templates are not used for RVT output.
- Name - use the default file name or specify your own. The default uses the assembly name and adds a suffix.
- Location - Sets the location of the new file. To find the part when the assembly is opened, specify its directory by a path in the project used for the assembly.
- BOM Structure - Sets the BOM structure for the component, Normal is the default.
Note: You can override the structure to be Reference at the component instance level.
Note: Not used for RVT output.
- Structure - used only for RVT output, choose the desired Structure option:
- Style is used for IPT output, provides up to four choices.
Note: Not available for RVT output.
- Advanced Properties provides other settings that help manage the simplify output.
These are the general settings:
- Break link to break link between the parent assembly and the simplified part.
Note: Not available for RVT output.
- Suppress link to suppress link between the parent assembly and the simplified part.
Note: Not available for RVT output and when the
Break link box is checked.
- Rename simplified components. The following items are renamed:
- Fill internal voids to fill all internal void shells in the simplified solid body part.
- Remove internal parts selected by default. Inventor looks at the model from 14 standard directions (six orthographic and eight isometric) to determine a parts visibility state. Parts deemed not visible are removed.
- Use
Link face color from source component to link color from the source component into the target part. If deselected, the appearance is set to default appearance of the target part.
- Make independent bodies on failed Boolean to create a multi-body part when a Boolean operation fails on one of the single solid body style options. Available only when Style is Single body with no visible edges between planar faces or Single body with visible edges between planar faces.
Note: It is possible to produce gaps when small faces are removed. If gaps are present, the result is a non-manifold body.
Note: Not available for RVT output.
Note: All internal voids are automatically filled.
- Use
Create model parameters to create three read only parameters for the "Edge A", "Edge B", and "Edge C" are created in the simplified file parameters window.
- Click
OK to create the simplified part from the specified criteria.
To Edit a Simplify Substitute
Substitutes are model states based on a simplified model. They are added to the assembly and placed in the Model States Substitutes folder. To edit the simplified substitute:
- In the browser, expand the
Model States
Substitutes folder.
- Right-click the Substitute you want to edit and click
Activate. The model updates to display the substitute.
- In the browser, right-click the substitute model and click
Edit.
- In the browser, right-click the and select
Edit Simplified Assembly.
- In the property panel, modify any of the following as needed:
- Initial State - select a different model state, design view, or position view
- Envelopes
- Components - include or exclude additional parts
- Features - add or refine the parameters for features being removed
- Output
Style
- Click
OK. The substitute updates.
Easily Identify a Substitute or Simplified Assembly
Whenever a part or assembly is created to be a substitute component, the context menu for that component displays a read-only status called Substitute. When the Substitute is checked, the part or assembly is a substitute model. Therefore, all part files have the Substitute status. It is checked ONLY if the component was created as a substitute component.