The Side feature provides low-level manufacturing control when you need customized manufacturing that is not addressed by either the Boss feature or the Pocket feature.
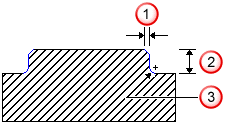
— Chamfer
— Depth
— Bottom radius
The Side feature is useful for:
- Outside part boundaries where the Side feature has special attributes for controlling the starting point of the cut and for controlling the region that is cut.
- Features defined by open curves have endpoints which do not meet.
The region that is cut for a Side feature is controlled by one of the following:
- The stock boundary, which is extracted automatically for you if you do not explicitly specify a
Stock Curve.
- The
Stock Curve that you provide for the Side feature.
- The offset distance specified by the
Total Stock attribute.
If you set the
Total Stock attribute to a positive number, then a roughing pass and finish pass are performed in the region between your Side feature and a curve offset by the
Total Stock value. To perform only a single pass around your feature, set the
Total Stock attribute to a positive value and set
Finish Allowance to
0 to turn off the finish cut.
Warning: Do not create a Side feature from a curve that extends more than a tool radius from the stock boundary. The manufacturing of these features is unpredictable. To correct this problem, move your curve onto the stock boundary or to within a tool radius of the boundary.
If you use a Side feature with a
stock solid, the toolpaths are trimmed to the stock to prevent air cutting.
FeatureCAM follows this general process to create a Side feature:
- Conducts an analysis of the curve and using tool diameter and length as the selection criteria, selects a tool from the current tool crib. The most important criteria are diameter and length.
- For tool diameter,
FeatureCAM analyzes the curve that defines the Side to determine what size tool to use. The smallest corner and tightest passage determine the largest tool that can cut the Side without gouging (See
Tool % of arc radius).
- For tool length
FeatureCAM picks a tool that has flutes long enough to cut to the bottom of the side.
- Chooses feeds and speeds for all of its milling using the
Feed/Speed database that you can customize. Feeds and speeds are determined based on the stock material.
- Generates a roughing pass, possibly in multiple Z steps based on the depth of the Side feature.
The important aspects of roughing are:
-
Getting to depth — The tool must get to depth, and this is accomplished by a zigzag in Z (the default setting and influenced by
Max ramp angle), by plunging, or by predrilling (see
Pre-drill diameter and
Pre-drill point). For open curves,
Lead distance and
Lead in/out angles control the horizontal approach to the material.
-
Vertical step —
FeatureCAM's cut depth is no more than 100% of the tool radius (see
Rough depth of cut and
Rough pass Z increment).
-
Horizontal stepover —
FeatureCAM moves over laterally a percentage of the tool diameter (controlled with
Rough pass %) as it steps across the feature.
-
Finish allowance — The rough pass contains a
Finish allowance attribute which controls how much material to leave for the finishing pass. By default this is
0.02.
- Generates a finishing pass. By default, the bottom is not finished. The roughing tool removes all of the material in Z. This is controlled by
Finish bottom.
-
Tool selection — After the roughing pass, the roughing tool is used to finish the side.
Use finish tool commands
FeatureCAM to choose a separate finishing tool (that has the same characteristics unless you override them).
-
Ramp on — The finish pass ramps into the material with an arc equal to a percentage of the tool diameter (see
Ramp diameter). For open curves,
Lead distance and
Lead in/out angles control the horizontal approach and exit from the material.
-
Finish passes and overlap — The tool goes across or around the side a number of times set by
Finish passes, and overlaps the starting point by an amount controlled by
Finish overlap.
-
Ramp off — Uses another arc of the same size as the
Ramp on to move the tool away from the finished wall.
-
Retract — Removes the tool from the stock area and sets up for the next operation.
You can edit this process in these places:
- To edit all instances of this type of feature in the current document, use the
Machining Attributes dialog.
- To edit a single feature, use the
Tools,
Milling,
Strategy, and
Misc. tabs for the feature in the
Feature Properties dialog.
The tooling database also has a large impact on how a feature is machined, and the feed/speed database helps to determine the feeds and speeds used.