Click to manage the materials in the library. Users can create new materials, delete unwanted ones, and duplicate a material as a basis for defining a new one.

Sample plot of plasticity for Inconel 625
When creating a new material, first specify the name, and then the various physical properties in the chosen system of units. To change the system of units shown here, go to the
, and open the
Units drop-down menu.
The
Show Plot button is available for temperature-dependent properties, to plot values displayed in the table.
Creating New Materials
There are three ways to do this: duplicate an existing material, import a material property file, or click the New Material button and manually enter the name and properties.
To duplicate a material and modify properties
- Select a material with properties similar to what you want in a new material, and click
Duplicate Selected. The material name is appended with ' - copy' to differentiate it from the original.
- Optionally, change the default name by double-clicking it and entering a new name.
- Modify the material properties as required. Note that properties having a table of values include
Add Row and
Delete Row buttons to facilitate modifications.
Some minimum requirements exist for material properties, depending on how the material is used:
- For
build plates, minimum requirements are Thermal Conductivity, Density, Specific Heat, Coefficient of Thermal Expansion, Elastic Modulus, and Plasticity properties.
- For
processing parameter (PRM) or directed energy deposition (DED) simulations, minimum requirements include those for build plates plus Thermal Emissivity, Latent Heat of Fusion, and Melting Temperature.
As material properties are entered for custom materials, the system evaluates whether they are within a physically realistic range, and replaces any erroneous values with acceptable ones. Stress Relaxation Temperature should be included for materials such as Ti-6Al-4V, which exhibits a significant sub–melting temperature reduction of stresses. If available, using as-built properties will produce more accurate simulation results.
Import New Material
Use this button to import a material property file in a .TXT or .CSV format. The material name must be unique in the material library, and should be in the file name, such as the example "Silver.csv". Any non-default material can be renamed by double-clicking the name in the material list. As the file is imported, it is checked for completeness and format, and the user is notified of any missing properties. For more information on formatting a material property file, see
Material Property Definition in
Local Simulation Help.
Best Practices
- Density - The model uses a uniform density. Temperature dependent density effects can be accounted for in the thermal model by adjusting the temperature dependent specific heat properties.
- Thermal Conductivity - Thermal conductivity should be provided to the highest possible temperature, preferably close to the melting temperature.
- Elastic Modulus and Poisson's Ratio - These values should be provided to the highest possible temperature. For metals without a known Poisson's Ratio, a generic value 0.3 may be used.
- Thermal Emissivity - Temperature dependent emissivity will produce more accurate model results, but can slow model convergence. Averaging temperature-dependent emissivities into a single value is an accepted practice.
- Thermal Expansion Coefficient - This property has the largest impact upon the accuracy of the mechanical model and should be included up to the highest possible temperature, preferably close to the melting temperature.
- Latent Heat of Fusion - Excessive values for Latent Heat of Fusion can cause poor convergence. If the thermal model fails to converge, check that this value is in the correct units and range, typically between 250-400 J/g.
- Melting temperature - Setting this value too low or high can negatively impact the accuracy of the predicted distortion results.
- Plasticity - Up to 10 pairs of stress-strain points can be used to describe the plasticity curve of the material at each temperature. Perfect plasticity is assumed after the final plasticity point at each temperature. Every temperature must use the same number of points. To enter the plasticity curve, specify the temperature, stress, and strain. Points with the same temperature will describe the yielding behavior at that temperature. For example using 3 points to describe the yielding behavior of a metal would look like this:

Different approaches for approximating the plasticity curve are shown in the figure below:
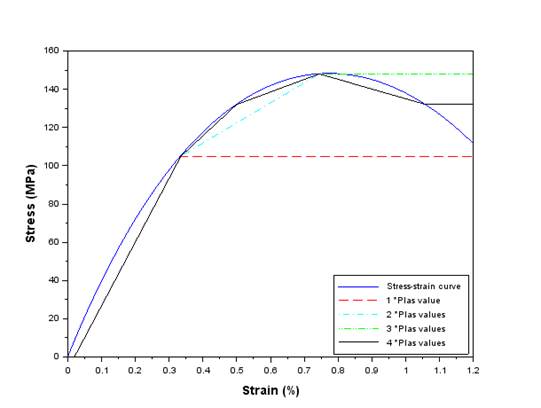
Using more points allows for a closer approximation of real material behavior, but can increased the computational time during moving source simulations, PRM generation, and models that enable
Structural Plasticity.
- Specific heat - Specific heat should be provided to the highest possible temperature, preferably close to the melting temperature
- Stress Relaxation Temperature – Should only be included for materials known to have significant sub-melting stress relaxation behavior.