Activity 1: Create a new thermal stress study
In this activity, you create Study 1 - Thermal Stress in which you
Change the Default Stress-free Temperature to 25 C
Set the mesh size to 6 mm
Verify the custom units system settings
Check that the model material is properly assigned. By default, the simulation study material is the same as the material defined in the Design workspace.
Note: The simulation units are independent of the units specified in the Design workspace.
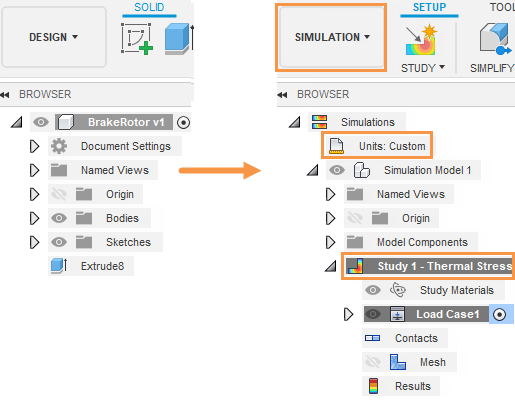
Browser when model is first imported (left). Browser after creating a new thermal stress study (right).
Prerequisites
- Fusion is started.
- Data file location: Samples > Basic Training > 11-Simulation > BrakeRotor.
Steps
Open the starting shape model, BrakeRotor in the Z up direction, from the Basic Training folder in the Data Panel.
- If the Data Panel is not currently shown, click
Show Data Panel at the top of the screen.
- The top level (home view) of the Data Panel is divided into two subsections: ALL PROJECTS and SAMPLES. Scroll down until you reach SAMPLES.
- Double-click the Basic Training folder to open it.
- Double-click the 11 - Simulation folder to open it.
- Double-click the BrakeRotor model to open it in the canvas.
Note: The sample model is read-only, so you must save a copy of it to a personal project.
Identify a personal project in which to save the starting shape models.
- Click
File > Save as.
- Enter a name, such as BrakeRotor, in the name field.
- Expand the arrow button next to the Location field.
- Locate and click on an existing project, or click New Project to start a new project.
Identify or create a folder in which to save the starting shape models.
- Double-click on a folder in the project to select it, or create a new folder.
- To create a new folder, click New Folder.
- Type a name, such as BrakeRotor for the folder.
- Press Enter.
- Double-click the folder to make it the current file saving location.
- Click Save
Select Thermal Stress as the new simulation study.
- Click on the Change Workspace drop-down menu at the top left end of the toolbar and select Simulation.
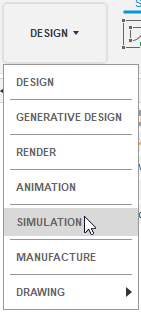
- In the New Studies dialog box, select
Thermal Stress
Change the Default Stress-free Temperature to 25 C.
- In the upper right corner of the large thumbnail image, click the
Settings icon to access the Settings dialog.
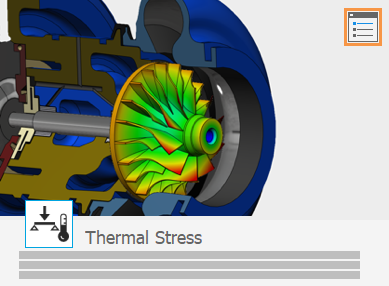
The General settings appear initially.
- Ensure that Remove rigid body modes is NOT activated.
This option is applicable only to unconstrained models. In this study, you apply constraints.
- Set the Default Stress-free Temperature to 25 C.
Set the mesh size to 6 mm.
- In the Fusion settings dialog, select Mesh from the left frame of the dialog to display the mesh settings.
- Click Absolute Size and type 6 mm in the input field.
- Click Back to apply the changes.
- In the New Study dialog, click Create Study to create the study and close the dialog.
Verify that the custom units system is defined as listed in the following table, and change any that differ:
Dimension | Units |
---|
Length | mm |
Mass | kg |
Time | s |
Force | N |
Pressure | MPa |
Temperature | C |
Energy | J |
Power | W |
Acceleration | m/s^2 |
Angle | deg |
- In the Browser, hover over
Units then click
Edit.
- In the Units Settings dialog, choose Custom from the Default Unit Set drop-down list.
- Compare the units settings with the table, and change any that differ.
- Click OK to accept the change and close the dialog.
Check that the brake rotor material is Iron, Gray Cast ASTM A48 Grade 20. Cast iron is commonly used for brake rotors due to the thermal characteristics of the material.
- Click
(Simulation workspace > Setup tab > Materials panel > Study Materials) to open the Study Materials dialog.
- In the Study Materials dialog, check if the value in the Study Material column is Iron, Gray Cast ASTM A48 Grade 20 .
Notice: The Model Material is already defined as Iron, Gray Cast ASTM A48 Grade 50. Additionally:- The default Study Material setting is (Same as Model).
- The default Safety Factor setting is Yield Strength. Safety factor results are based on the ratio of the yield strength to the von Mises stress. A minimum safety factor greater than 1.0 indicates that the part does not deform permanently under the assumed conditions.
Keep these default settings.
- Click OK to close the Study Materials dialog.
Activity 1 summary
In this activity, you switched to the Simulation workspace to create a Thermal Stress study, and then you defined its parameters. You
- Changed the Default Stress-free Temperature to 25 C
- Set the mesh size to 6 mm
- Verified the custom units system settings
- Checked that the model material was properly assigned.