Passive Cooling: Internal, Sealed
Components within a sealed, passive device are cooled by natural convection, conduction, and radiation. Temperature variations in the air cause density gradients, which in turn cause the air to move. Air cannot leave the device, so all heat transfer occurs through the casing. The air movement, conduction, and radiation transfer heat from heated components to the surrounding environment.
Flow in a passively cooled, sealed device is often laminar, and radiation plays an important part in removing heat.
Applications
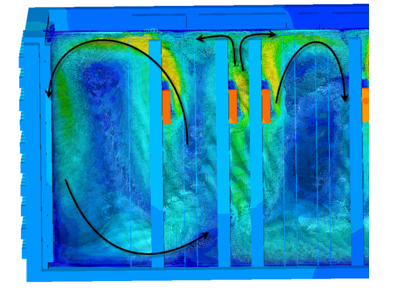
Router
Automotive:
- Under-dash electronics
- Instrument Panel electronics
- Under-hood components
- Hybrid system electronics
Military applications
Modeling Strategy
- Simplify the geometry to remove extraneous features. Simplify or rebuild sheet metal parts to remove detail that is not relevant to the simulation.
- The model must contain an air volume within the device. This is a consideration because the physical model probably does not contain one. Autodesk® CFD automatically creates an internal volume if the geometric model is "water tight." If not, modify the CAD model to close any gaps or use the Void Fill tool to create the volume on the Autodesk® CFD model.
- Be sure to include the external casing of the device.
Materials
- Because buoyancy drives the flow, the air material properties must be allowed to vary.
- Assign Air, and set the Environment setting to Variable.
- For very thin enclosures, the heat transfer is largely dominated by thermal conduction instead of convection. In certain applications, it is possible to accurately simulate the heat transfer without having to solve for the flow. Create a custom solid material that has the same properties as air. For more about using the "solid air" material...
- If radiation is included, specify emissivity for the fluid and solid materials. (Note that the emissivity specified for the fluid material only applies to the solid and wall surfaces that the fluid touches.)
- Use material devices to simulate objects such as baffles, internal fans, printed circuit boards, compact thermal models, and thermal electric devices. For more about using material devices...
Boundary Conditions
- Apply a Total heat generation boundary condition to components that dissipate heat.
- To simulate heat transfer to the surroundings, apply a Film Coefficient boundary condition to the external surfaces. The value depends on the air that surrounds the physical device:
- If the air is still, use a value of 5 W/m²K.
- If the air is moving, use a value of 20 W/m²K.
- Use a Reference Temperature = ambient temperature.
Mesh
A basic guideline for a high-quality analysis model is that the mesh distribution be sufficient to resolve the flow and temperature gradients efficiently. In regions where the flow circulates or experiences large gradients (such as in wakes, vortices, and separation regions), a finer mesh is required.
For most models, use Automatic Sizing to define the mesh distribution. It may be necessary to locally refine the mesh on geometric features that are highly detailed. For more information about Mesh Autosizing and model preparation...
In some cases, it may be necessary to adjust the Minimum Refinement Length to reduce their effect on the overall mesh count.
To locally refine the mesh in high-gradient flow regions:
- Adjust the mesh distribution on geometric volumes and surfaces.
- If there are no appropriate geometric features in a particular region, create a mesh refinement region:
- Add one or more volumes in the CAD model.
- Create a Refinement Region from the Meshing task.
Running
Flow = On
Heat Transfer = On
If the component temperatures are relatively high, Radiation = On (Radiation often has a stabilizing effect. In some models, neglecting the effects of radiation produces temperatures roughly 20% higher than actual values.) A useful strategy is to run 200 iterations without radiation, and then enable radiation and continue. This reduces the analysis time, and provides insight into the effects of radiation. Be sure to specify appropriate emissivity material property values. For more about modeling radiation.
Specify a Gravity vector.
Turbulence: The flow in these applications is usually laminar. Click the Turbulence button on the Settings dialog, and select Laminar. If the solution diverges within the first 100 iterations, select the K-epsilon model, and restart the analysis from iteration 0.
Results Extraction
Flow Distribution
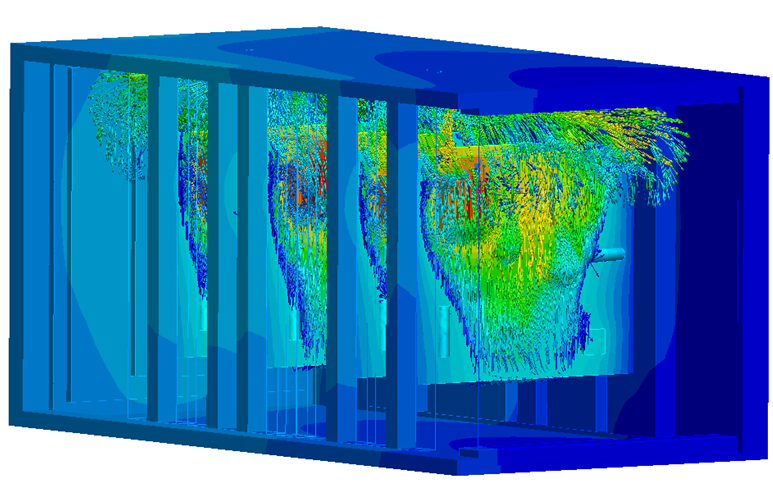
Component Temperatures

For more general information, use the extensive collection of results visualization tools to extract flow and thermal results.
Things to Avoid
- Do not neglect the effects of radiation, especially when component temperatures are high. Radiation is an important heat transfer mechanism for these applications, and without it, component temperatures may be over predicted. Note, however, that radiation requires more computational resources, so it is important to remove unnecessary geometric features from the model.
- Do not neglect component conduction paths. Heat cannot be conducted from a component that is floating in space. Be sure that physical connections between components and other objects are included in the model.